Understanding Straight Axles
Many historians agree that the wheel was invented in 3500 BC. What doesn’t get mentioned is that a wheel needs an axle in order to carry any weight. That means the straight axle has been around for just as long. When the automobile came about, the need to transmit power through the axle led to the invention of the live axle. The car axle still needed to carry the vehicle weight, but it also had to transfer power to the wheels, so the live axle design made a lot of sense. Any time you can have a single component do multiple functions it’s an engineer’s dream. That’s why you can still find straight axles under cars and trucks today. There are plenty of independent designs in use, but when the load capacity goes up, the live axle gets called into duty. The straight axle design is popular because it has many attributes that can’t be beat.
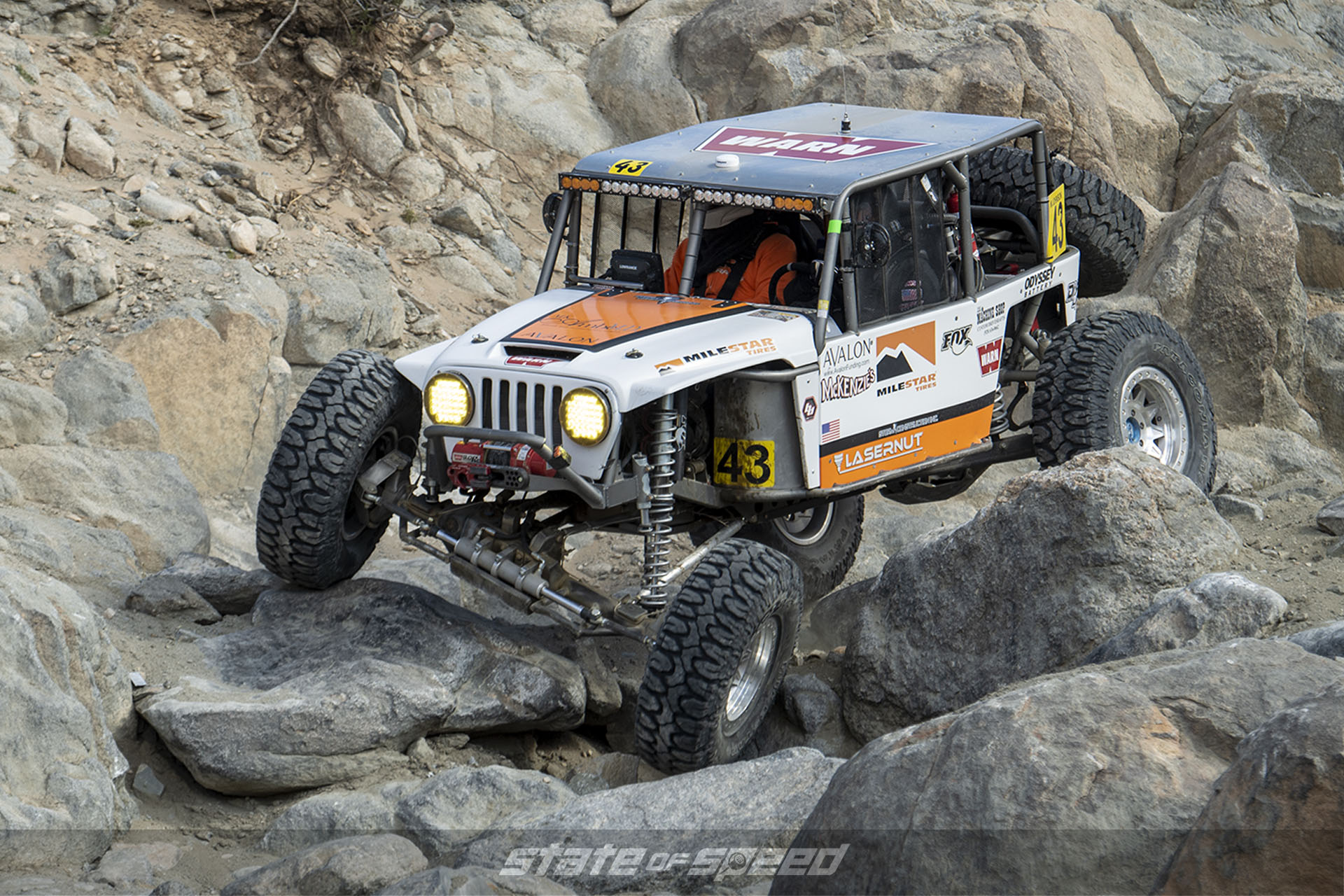
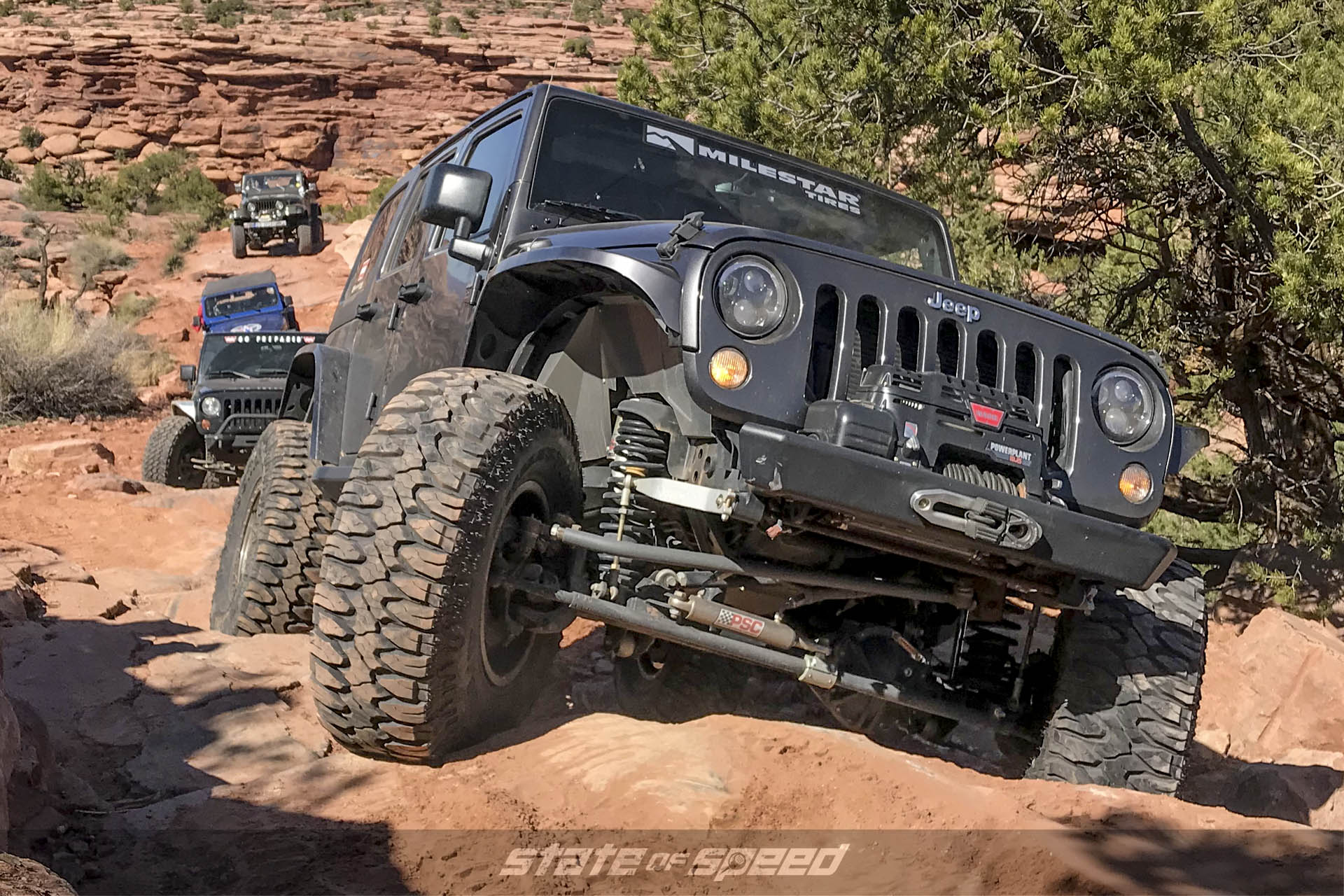
Tires: Patagonia M/T
Strength
If you look at the individual parts that make up the straight axle assembly you will see that they are large, and stout. The housing is a weight bearing assembly so the axle tubes are generally a large diameter. The physical size is needed to allow room for the axles inside, but they also give strength to the overall housing. As the weight capacity goes up, so does the diameter of the axle housing tubes. Some of the largest live axles available are the military 5 ton units. Their axle tubes are actually square. They have plenty of room inside, even for the 2 inch diameter axle shafts they use.
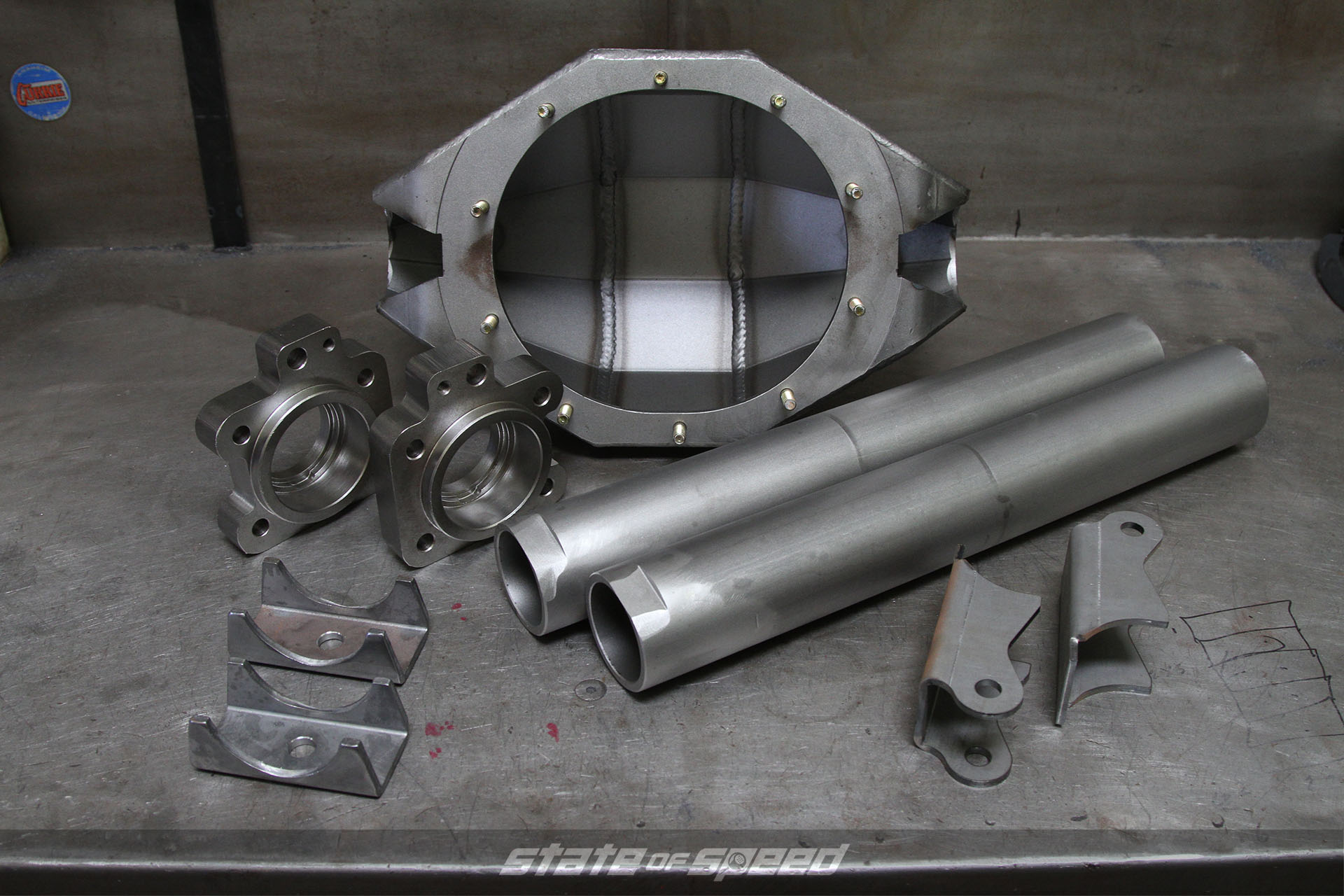
All the power from the engine goes down the driveline and through the axle shafts, so as the intended loads increase, so does the diameter of the axles. The center section that houses the gears is most commonly made from cast iron. It needs to keep the ring and pinion from deflecting under load. During acceleration, deceleration, and cornering, the ring and pinion sees forces from several directions. If the ring and pinion were able to move at all, the mesh between gears would vary, and create binding, and irregular wear.
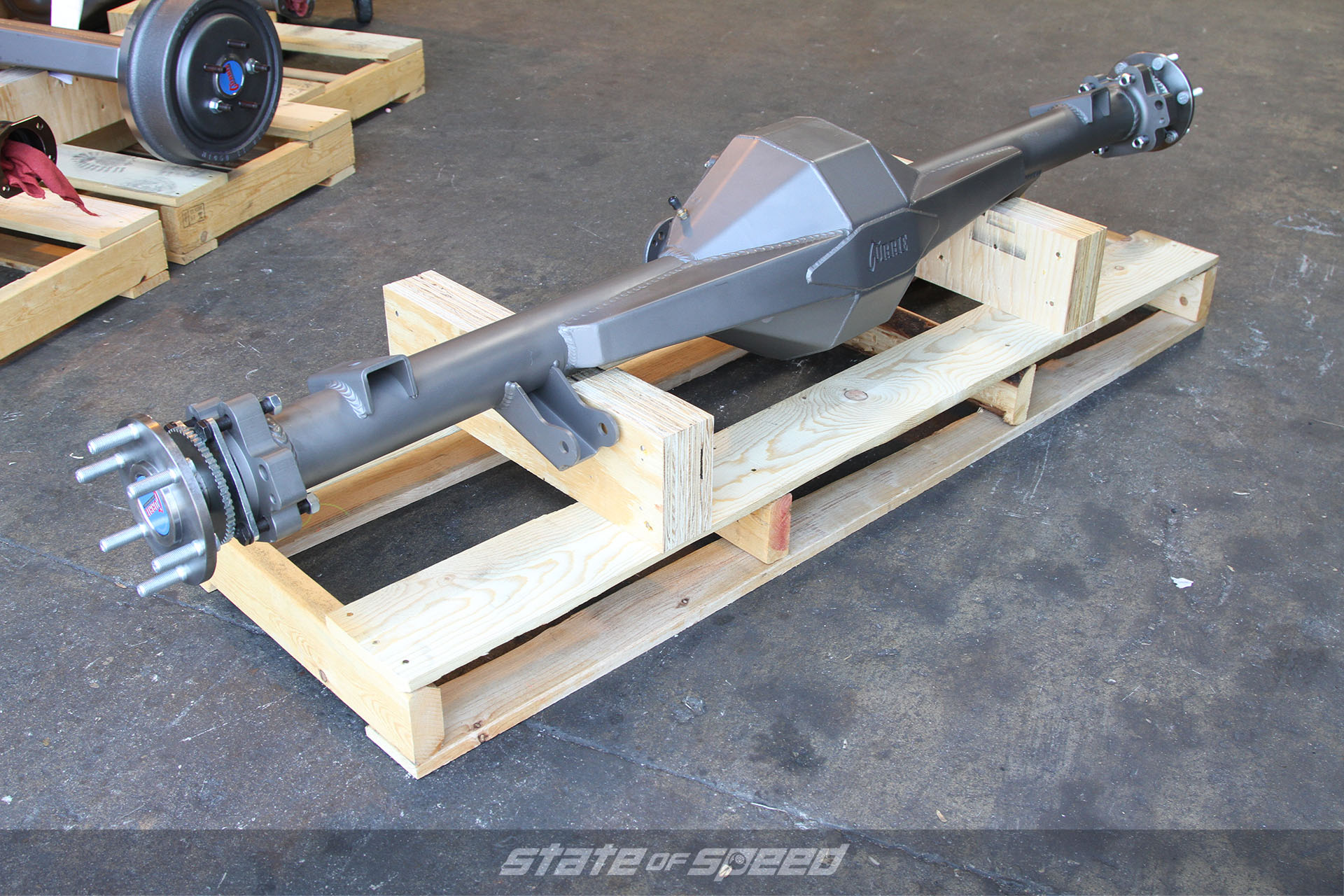
Most live axles are the same design, but scaled up or down to fit the parameters. A small, lightweight suv will not need the same strength that a one ton truck or race vehicle requires. As the housing, axles, and gears get bigger, the remaining parts all need to increase in size as well. Because of the straight axles design, it is easy to attach suspension mounts, and to increase the axle housings strength with the use of thicker materials and/or additional gusseting. This gusseting can be pretty extravagant on some configurations, and many are works of industrial art.
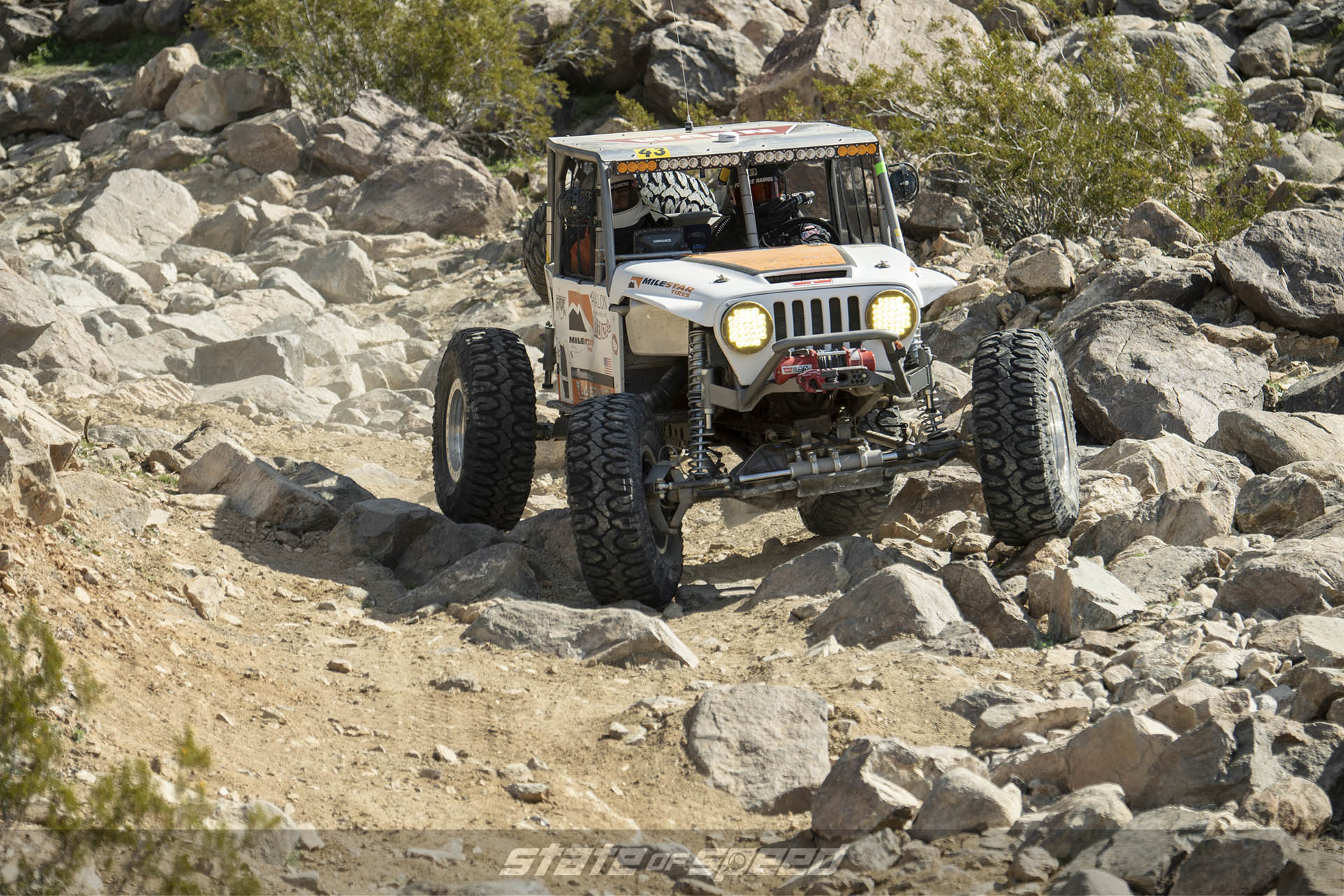
As seen on some Ultra4 cars, the center section can be moved to either side of the housing. The rear engine cars locate the center section all the way over to one side due to the location of the drivetrain. Auto manufacturers vary the location of the center section. Ford likes to locate it on the driver’s side in front axle applications. GM puts it on the passenger side. In the rear, it’s common to locate the center section slightly off center to compensate for the pinion gear offset. That way the axle shafts can be the same length.
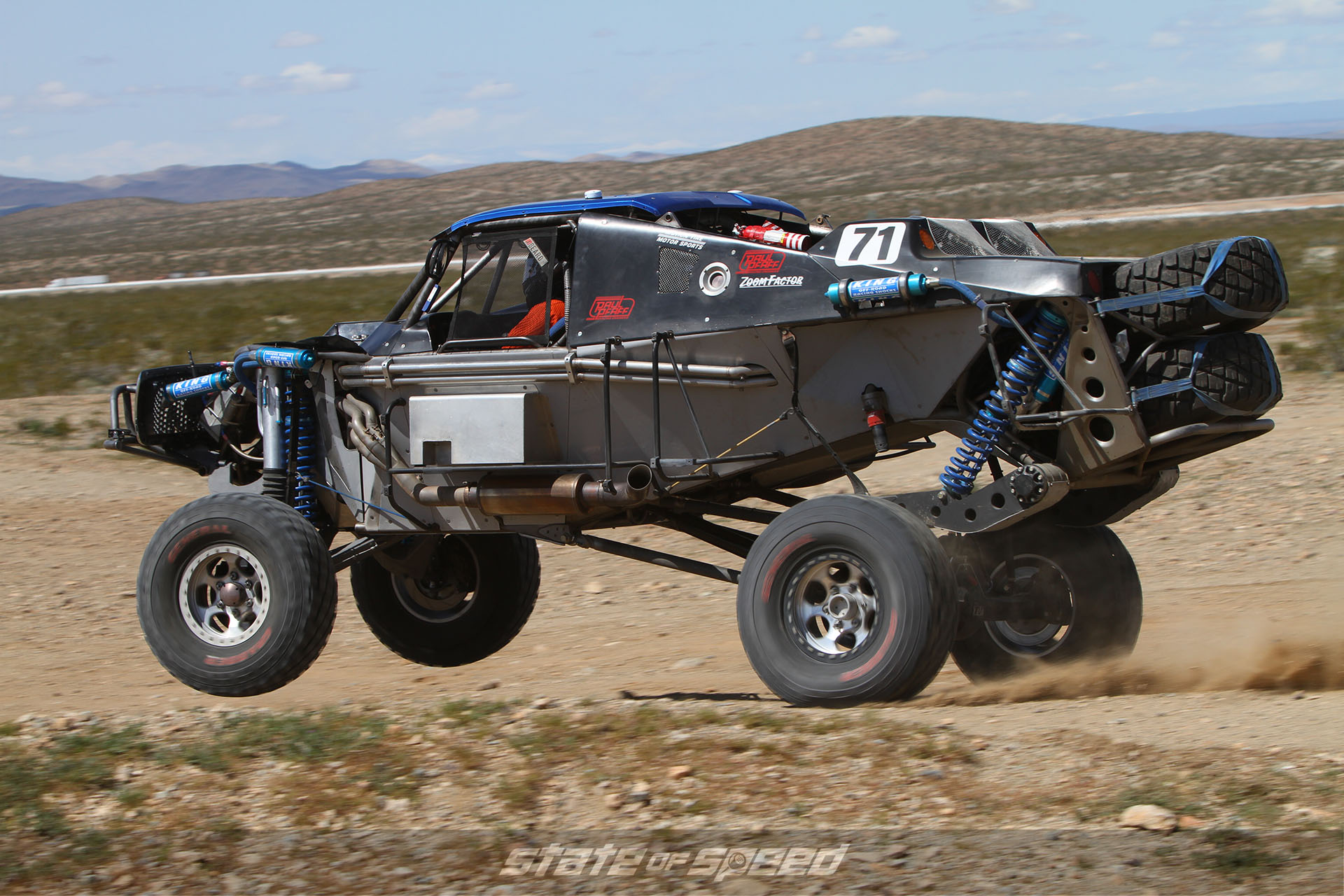
Versatility and Simplicity
The straight axle is simple in design, and extremely versatile. It can be used with many different suspension configurations. Leaf springs, coil springs, Torsion bars, or coilover shocks can all be used with the straight axle to suspend the vehicle. With leaf springs, the spring eyes provide the attachment points to the chassis. A coil spring, or coilover shock does not locate the axle so many different designs exist to attach the straight axle to the chassis including radius arms in front, links, or trailing arms and a wishbone.
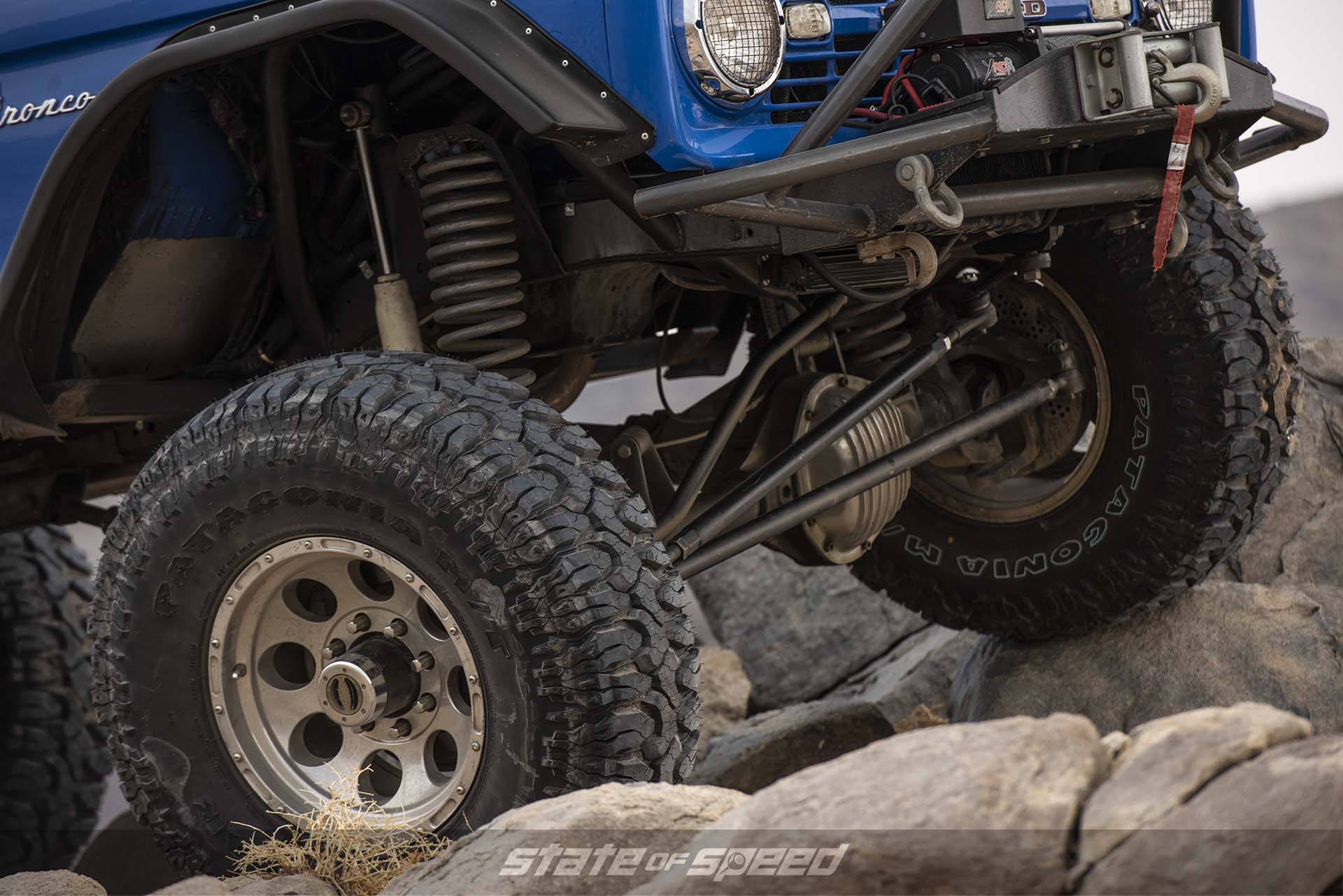
Tires: Patagonia M/T
Links can be triangulated to center the axle, or a panhard bar will be needed to control side to side motion. Still another straight axle suspension design is the watts link. The watts link keeps the rear axle centered at all times, which is good, but because of its equal length links, and center pivot design, the suspension travel is limited. Offroad race trucks use a wishbone or triangulated design because they use an incredible amount of suspension travel; up to 30 inches or more on some Trophy Trucks.
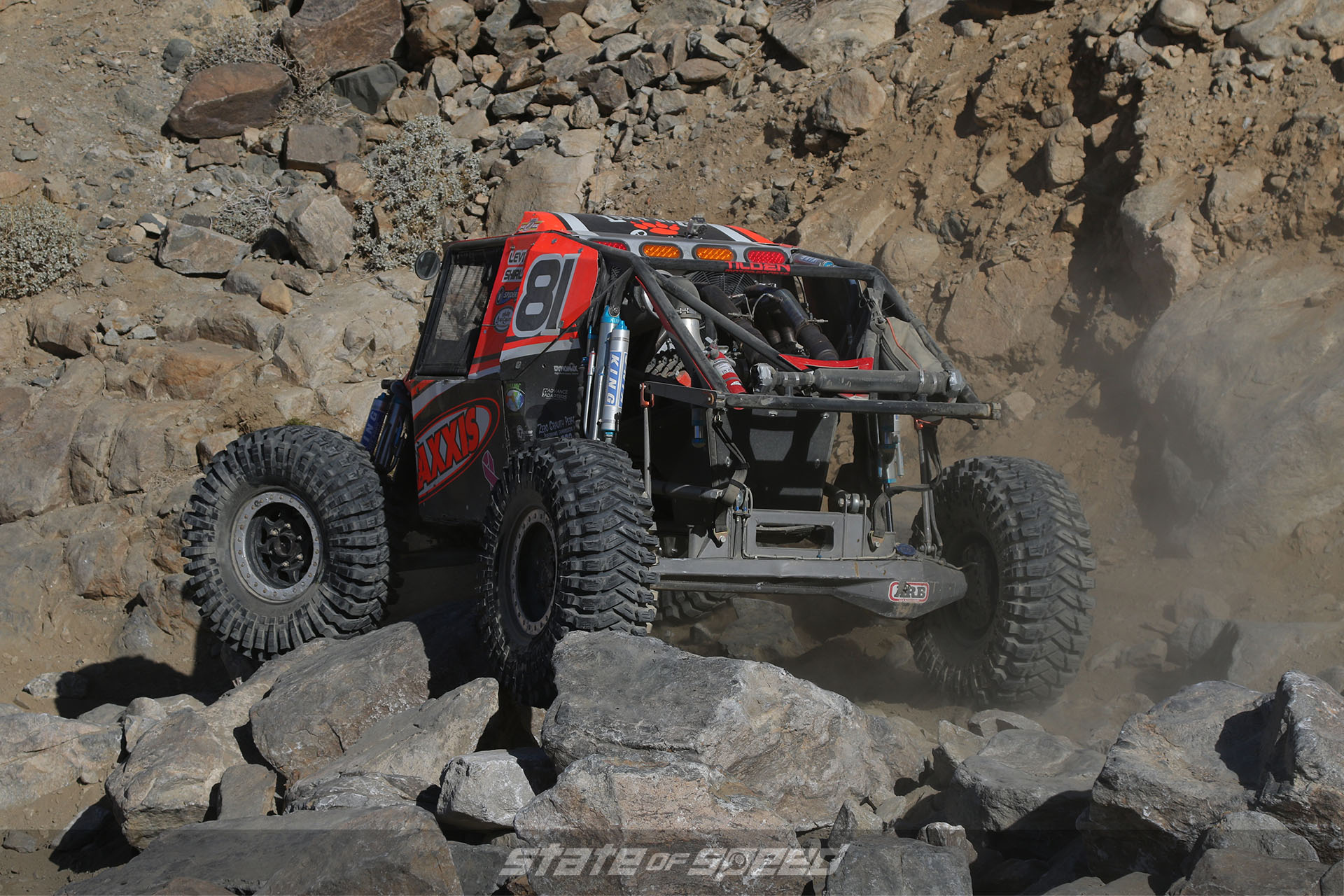
Performance
The straight axle is popular among rock crawlers because of the superior traction it affords. That traction is made possible because of the travel and articulation possible. We’ve already discussed the suspension travel possible, but articulation is also critical to maintaining tire contact with the ground. With a straight axle, as one side travels upwards, like when climbing over a rock, the opposite side is pushed down into the ground.
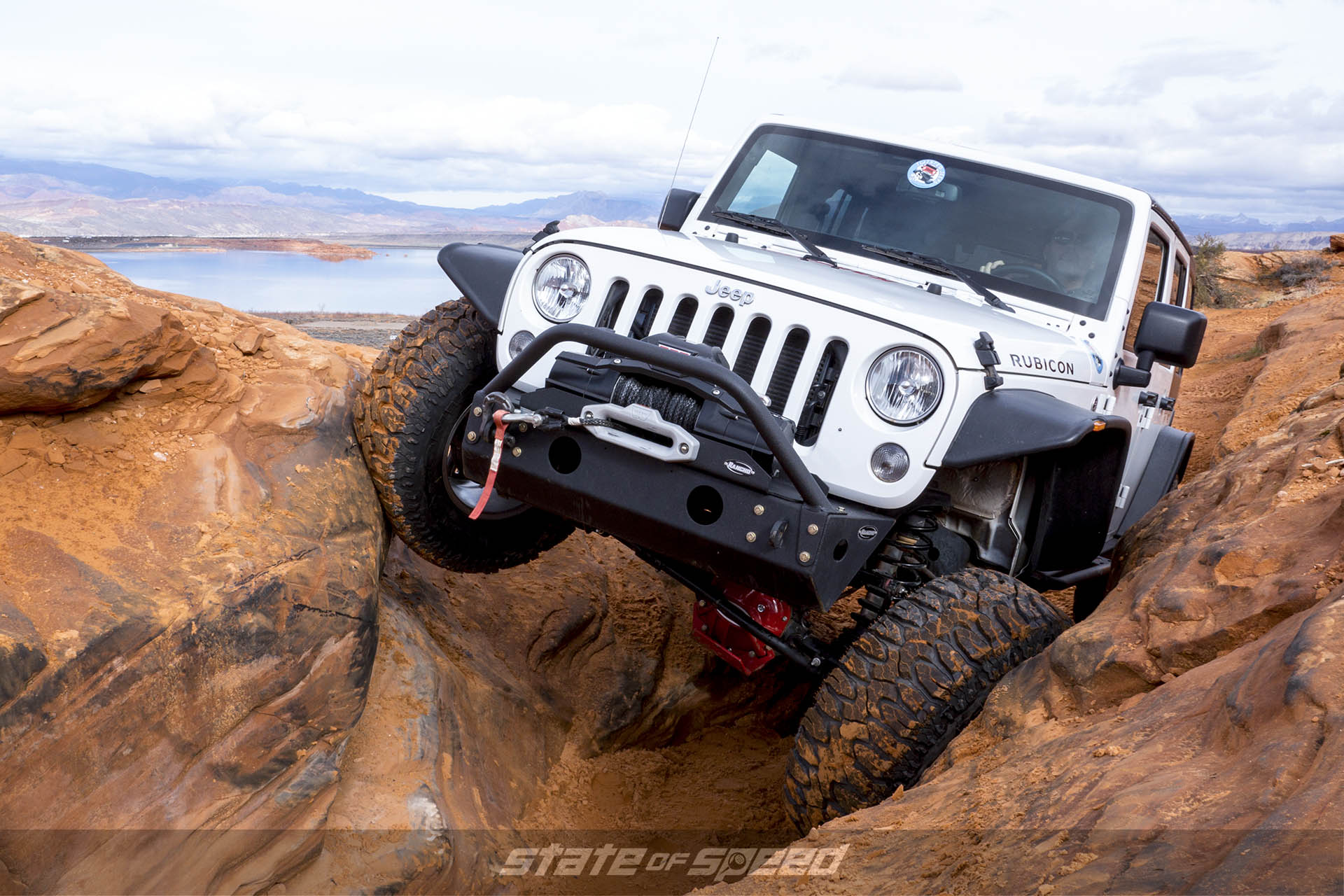
Tire: Patagonia M/T
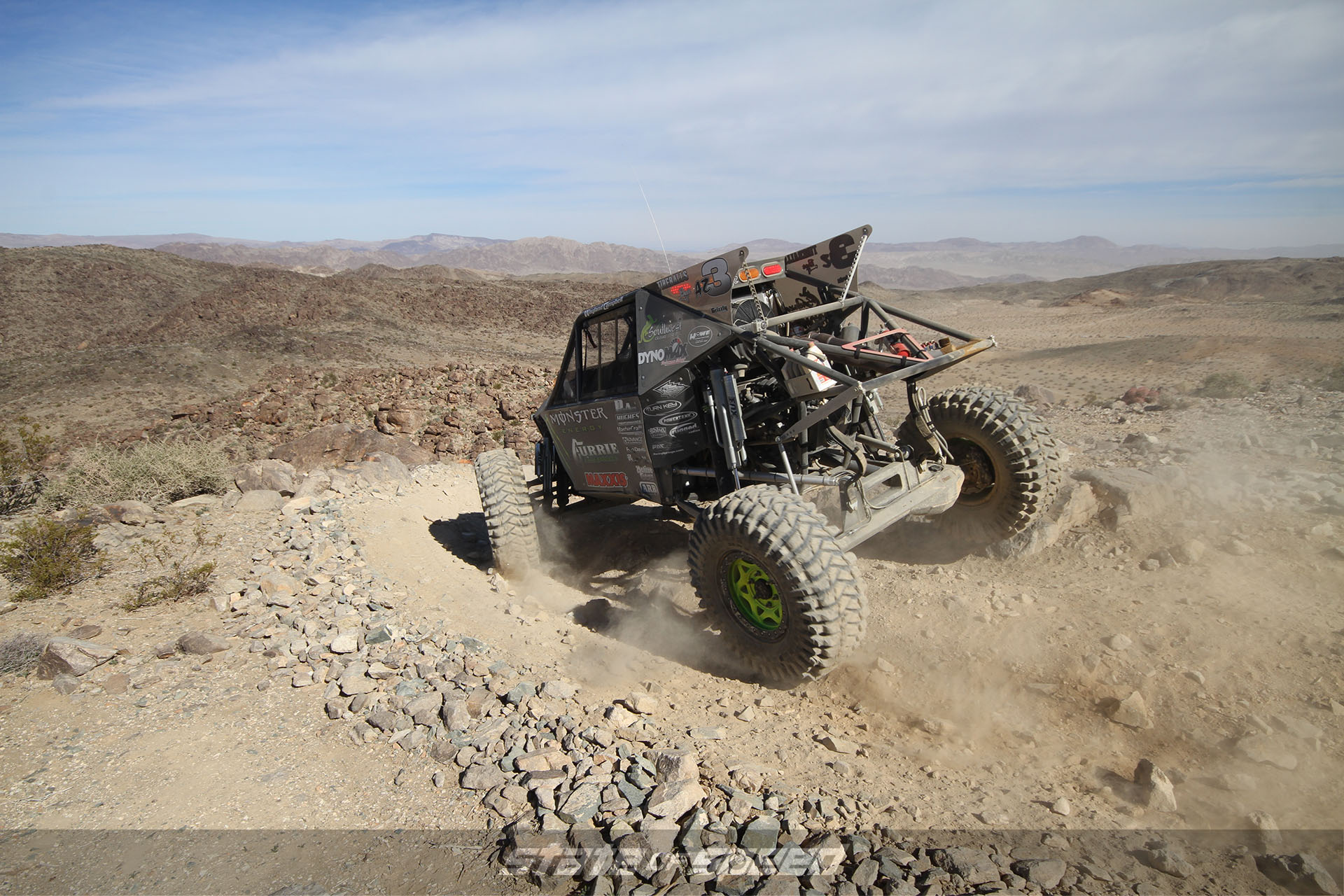
Both tires will be planted. In an independent design, as one wheel moves up, it lifts the entire front end. The opposite tire can be lifted off the ground when the travel limit is reached. Independent suspension travel is limited by the length of its arms, and the maximum angle possible from the CV joints.
With a straight axle, as one side travels upwards, like when climbing over a rock, the opposite side is pushed down into the ground.
The independent suspension is pivoting from the attachment point at the chassis. That distance from the pivot to the tire is less than half the width of the vehicle on a factory based truck. The straight axle will be pivoting at the opposite tire. That means the pivot point is as wide, as or wider than the truck. The longer the distance from the pivot point to the tire, the more travel you will have. Travel is the distance it can move up and down, Articulation is the distance between the tire moving up, and the opposite tire moving down. Suspension travel and articulation are related, but in the rocks, articulation is king.
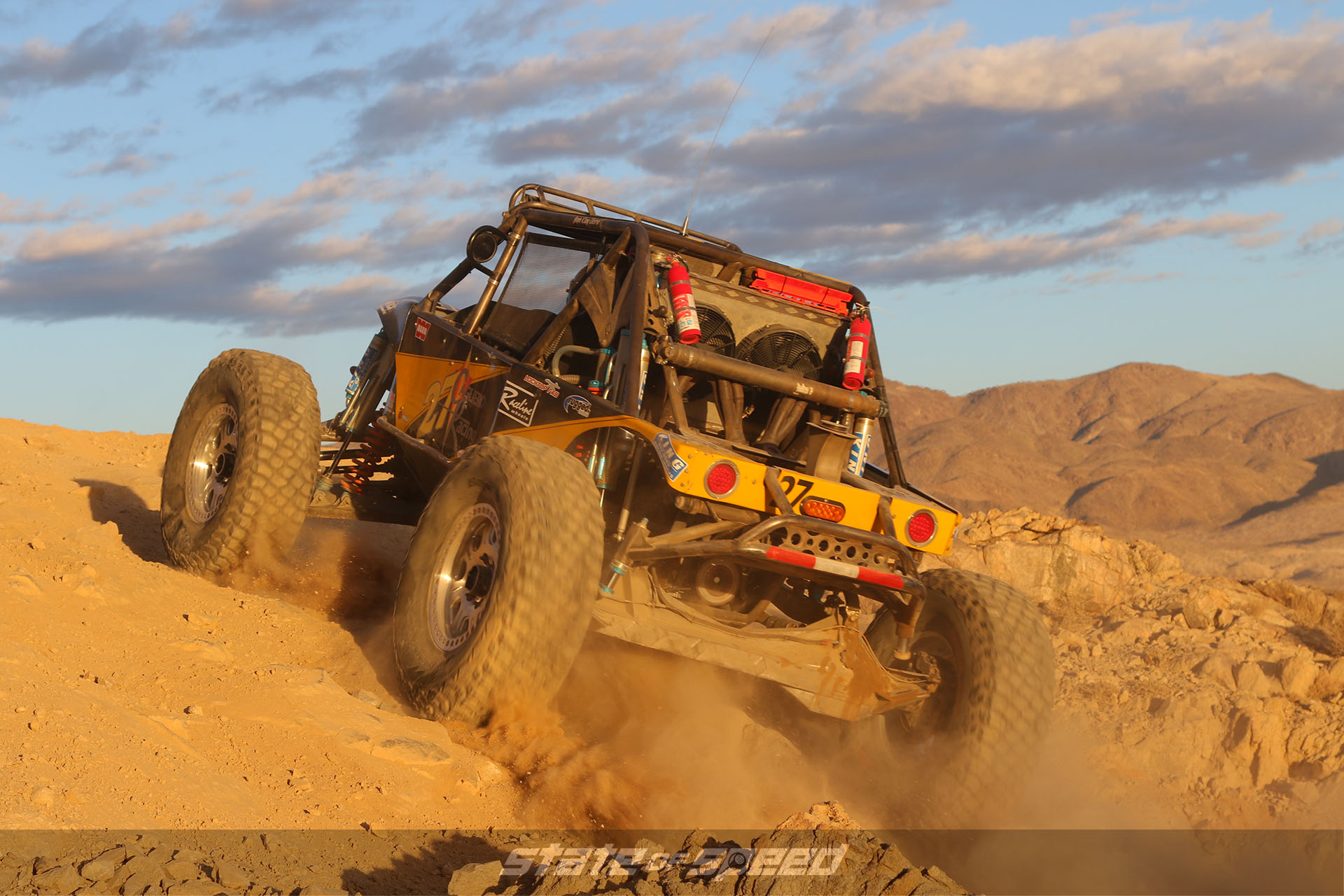
Downsides
The straight axle has some great attributes, but it also has some drawbacks. While one side of the axle affecting the opposite side is an asset in the rocks, it’s a drawback when it comes to a smooth ride. The entire axle is disrupted by input from either side. The strength afforded by those beefy parts comes with a weight penalty when it comes to unsprung weight. Sprung weight is the total weight of everything that is supported by your springs.
The more unsprung weight you have, the harder it is for the shocks to control that movement.
The body, the engine, the payload, etc. are all sprung weight. The suspension, brakes, wheels, and tires are all unsprung weight. Unsprung weight is in motion, and needs to be controlled by your shocks. The more unsprung weight you have, the harder it is for the shocks to control that movement. It’s easy to catch a tennis ball. It takes much more effort to catch a bowling ball. You can run bigger shocks with more valving, but you are getting additional stress and strain on the vehicle. For those people who love their straight axles, it’s a small price to pay. When it comes to strength, and simplicity, the straight axle is hard to beat.