Leaf Springs vs Suspension Links
Let’s be specific, and talk about leaf springs versus suspension links with a solid axle. You may have a straight axle in one end of your 4×4 or both, and it could have a combination of links with leaf springs, all leaf springs, or all links front and rear. Both leaf springs and suspension links have their strengths, and weaknesses. Depending on several factors, either design might be right for you, so we’ll take a look at both.
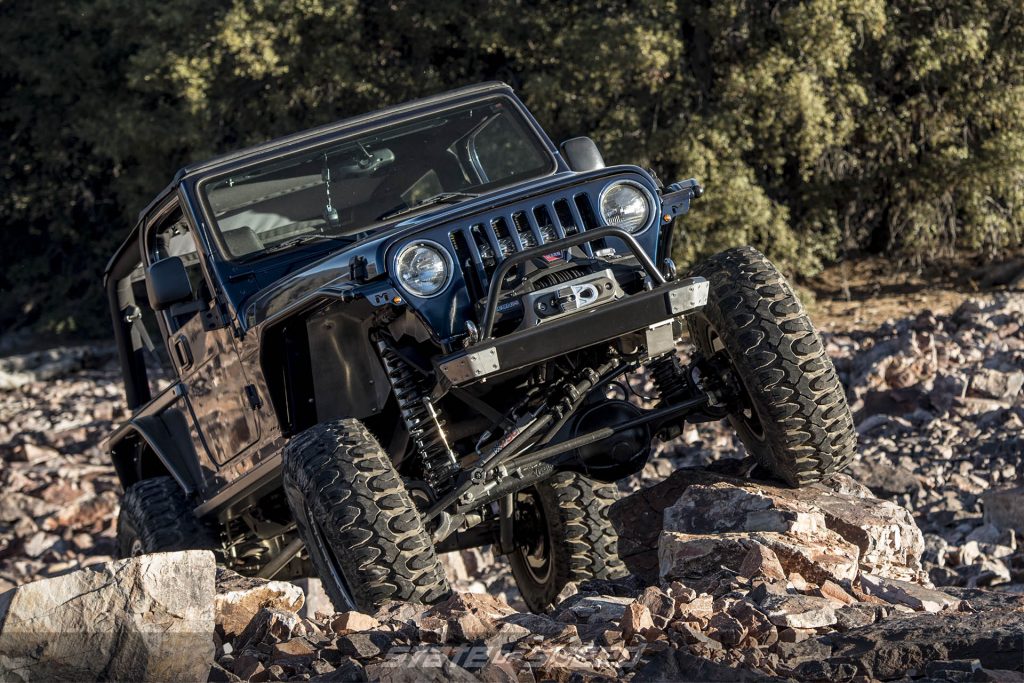
Tires: Patagonia M/T
There are all kinds of link configurations in use. Links can take the form of radius arms, be used in a combination of 4 links, or 3 links, and include wishbones, or panhard bars to center the axle. There is even a unique watts link design, but it is rarely used on a 4×4 because of its limited suspension travel. The job of the links are to locate the axle; that’s it. Some designs will have the shocks and/or springs mounted to the link, but that’s an added function. The link’s main role is to attach the axle to the chassis, and allow it to articulate.
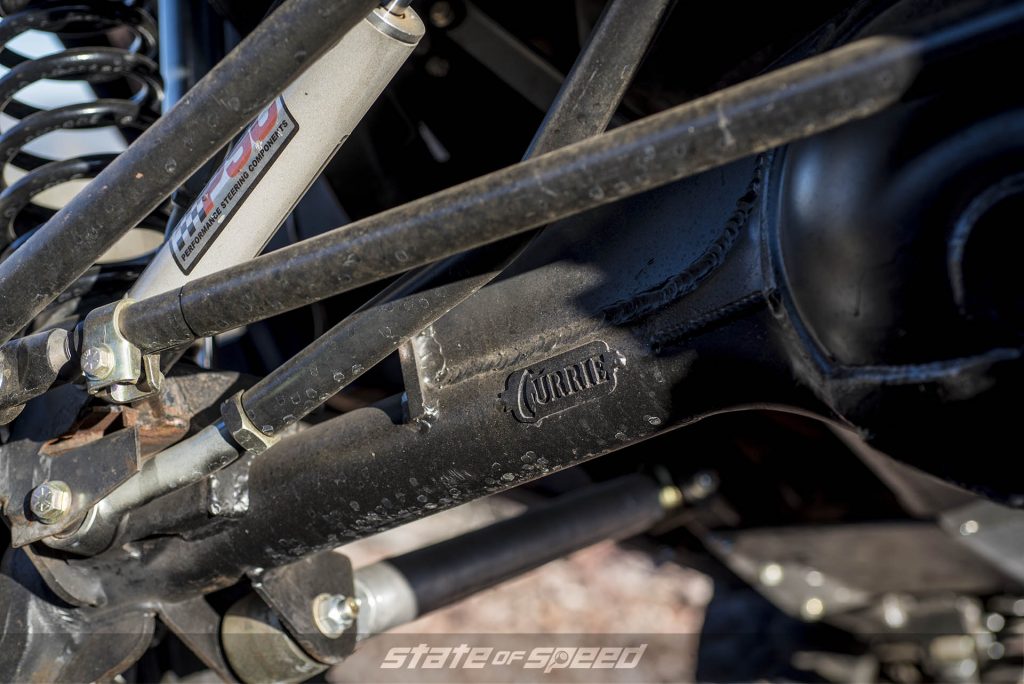
Linked designs use a coil spring to support the weight of the vehicle. Coil springs can be mounted independently of the shock, or they can be combined in a coilover shock. The coilover shock is a fantastic design because it is compact, and easy to mount. There are no spring retainers or coil buckets needed, only a single bolt on each end. The distinction of a coil spring is important because a coil behaves much differently than a leaf spring. First let’s talk about spring rate. The amount of weight it takes to deflect a spring one inch is the rate of the spring. If it is 100 pounds then for each inch the spring is compressed, it generates 100 more pounds of resistance. To compress it 2 inches, it takes 200 pounds of force. If the coil is wound consistently throughout its length, then it is a single rate coil. Its spring rate is linear. The 100 pounds per inch does not vary.
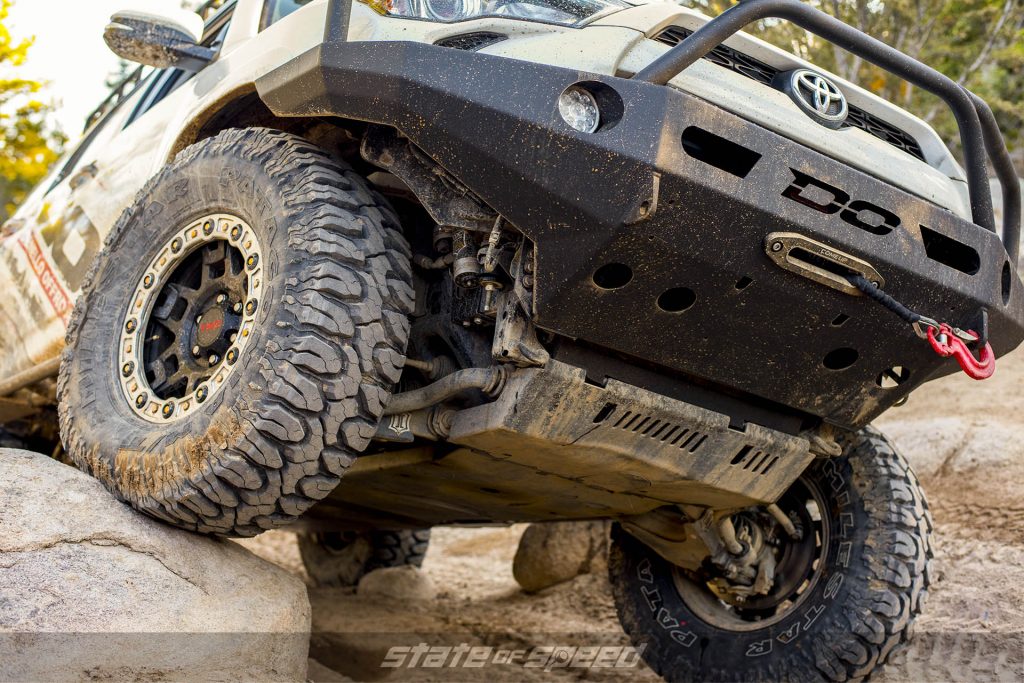
Tires: Patagonia M/T
Linked designs use a coil spring to support the weight of the vehicle.
There are progressive rate coil springs too. They have a few closely wound coils at one end and then wider, equally spaced coils at the other end. The closely wound coils compress at a different rate than the widely spaced ones. Dual rate coil springs are used in some factory based designs. With coilover shocks, the way to create a progressive spring rate is to stack them together. A short stiff spring stacked on a longer, more flexible spring will give you a spring combination that changes rate as it compresses. It’s easy to swap coils to fine tune the rate. You can also adjust the spring rate by introducing preload to the coil spring or springs. If you compress the coil one inch in our 100 pound example, the resistance will already be 200 pounds while the vehicle is at rest.
On a leaf spring, the rate is progressive due to the multi-leaf design. The more you compress it, the higher the rate goes. Leaf springs work together as a single unit. Each spring is designed to work with the next leaf in the stack. It’s much more difficult to adjust them without the entire leaf pack being removed, and disassembled. Leaf springs can also suffer from spring wrap. Under hard acceleration or braking, the spring can wrap around the axle causing the axle to twist. The twisting can negatively affect traction, and abruptly changes the pinion angle which strains the driveshaft u-joints. A linked suspension will resist this condition because the links don’t flex. With leaf springs, there is no way to introduce preload to the spring. For ease of tuning, the coil spring wins.
Leaf springs have been used since roman times so they are well understood.
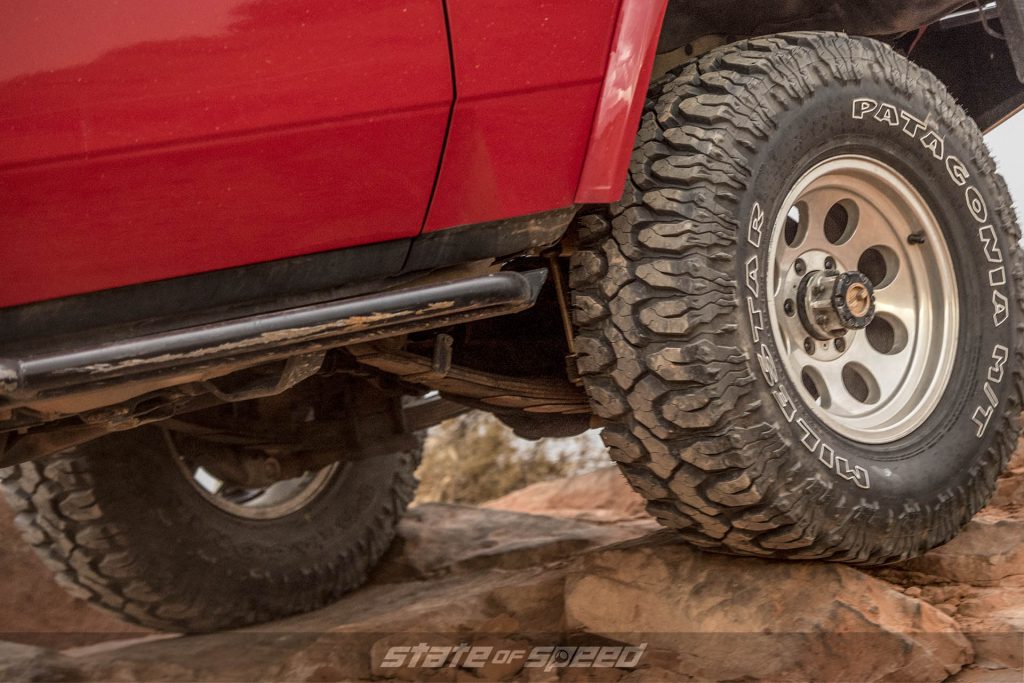
Tires: Patagonia M/T
The use of a coil is a huge advantage in the link design, but a linked suspension is much more complicated than the leaf spring design; especially if you are retrofitting it onto an existing leaf spring vehicle. It will take extensive fabrication, and a good understanding of suspension geometry. If you are building a 4 link design, the links take up a lot of space which means you will be doing extensive cutting, and relocating to make room. Most people who do a link conversion in the rear cut the entire back half of the frame off, and rebuild it from scratch to work with the link geometry. You can also forget about hauling much in the bed as that space is now taken up by the upper links. It depends on the link design you are using, but typically the longer the links are, the more suspension travel you can get. The linked design also offers more articulation. These attributes affect other assemblies on your vehicle like the steering linkage and the drive shaft, so they all have to be designed to work together. From a purely performance standpoint, the linked design wins again.
It would seem like a linked suspension is the way to go, so why are leaf springs still in use? Leaf springs have their own benefits that make them desirable. Leaf springs are simple to produce, and easy to mount. Leaf springs have been used since roman times so they are well understood. Not only do they support the weight of the vehicle, but they also locate the axle housing. They are very compact when compared with a link design. They are mounted towards the end of the axle housing for stability, so the room between the springs can be used for other components like the engine up front, and gas tanks in the rear. Those components can be located lower in the chassis to keep the center of gravity low to the ground. It also means that a truck bed or cargo area of an SUV can be roomier inside. Because of the leaf springs progressive spring rate, they are much better suited to supporting varying loads. If you drive your truck empty all week, but use a slide in camper on weekends, leaf springs can handle the variation with little or no modifications. The same goes for towing. The stability that a leaf spring design provides helps substantially while towing.
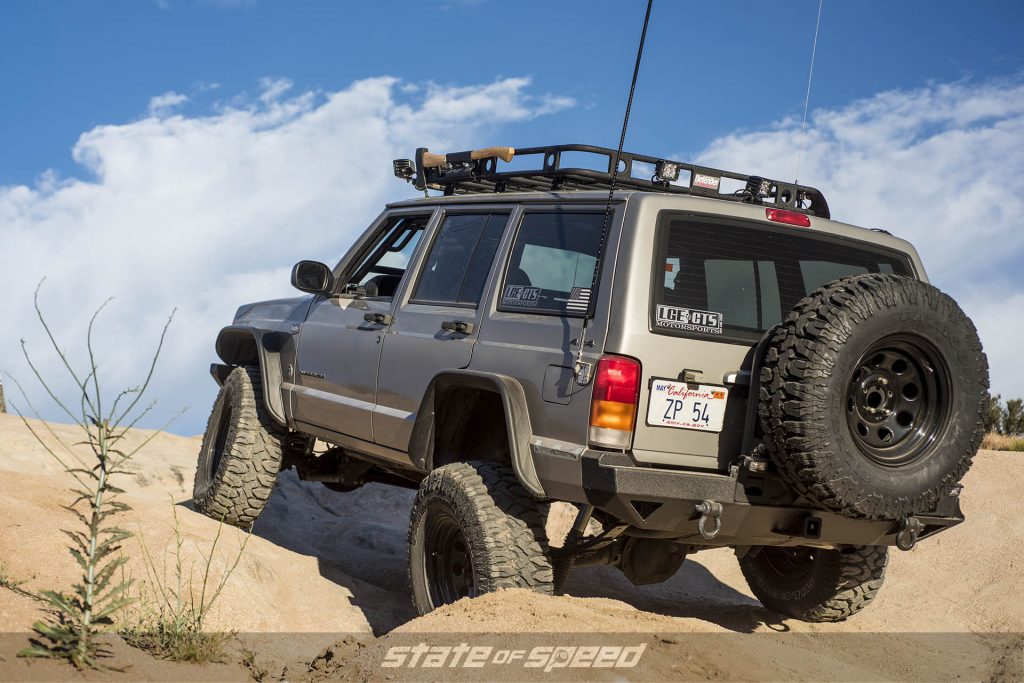
Tires: Patagonia M/T
If you want a performance based vehicle for rock crawling, or high speed running in the desert, a linked suspension is your best bet. If you need utility for towing, or hauling heavy loads, leaf springs are the way to go.