Lifting Your Rig 101: What to Consider
When the manufacturer sets out to design and produce the latest model four-wheel drive (4wd) vehicle, they are required to balance many factors from vehicle weight to carbon footprint. These constraints force them to choose components that meet the desired platform goals but typically leave little room before modifications exceed the strength of the factory components. With an estimated +300 billion dollars being spent in the light truck and SUV aftermarket in 2022, its safe to say there are plenty customers looking to upgrade their 4wd vehicles and one of the first modifications most owners make to a 4wd after purchase is to add some type of suspension lift and larger tires.
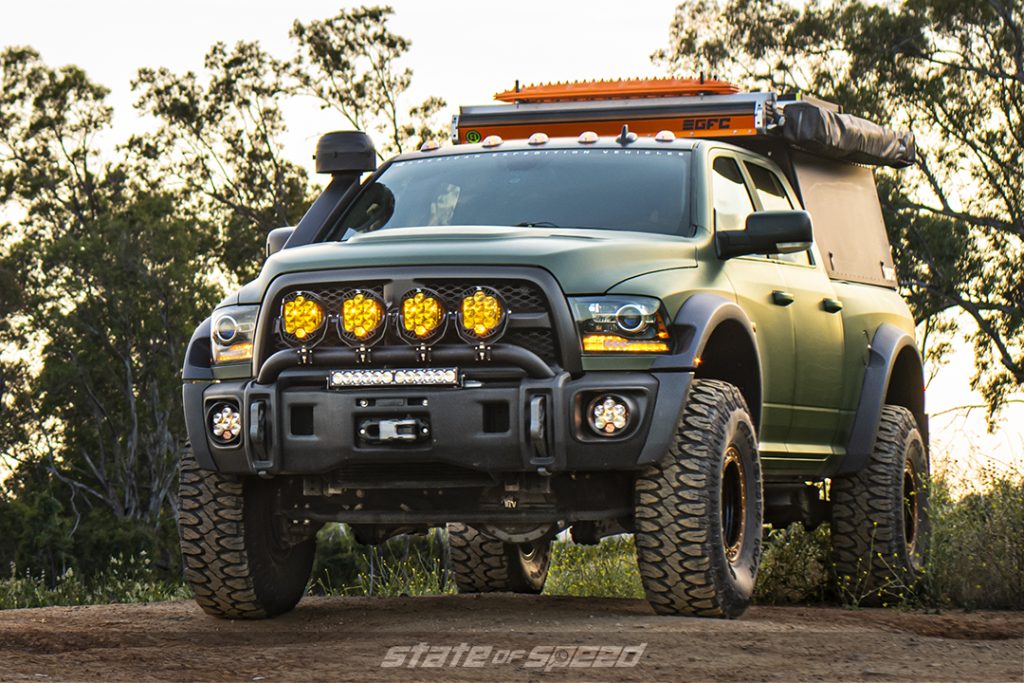
Tires: Milestar Patagonia M/T 40X13.50R17LT
For many, this is done merely for looks. For those who intend to use their newly purchased 4wd to take them on remote off-highway adventures or to tackle technical trails, a lift kit and larger tires is only the first step. What is soon discovered is that the additional tire size and weight create more stress on the suspension and drive axles. While most lift kit manufacturers take these additional factors into consideration during the development of the replacement suspension components, upgrading the drive axles for strength and performance is left up to the consumer to determine what and when.
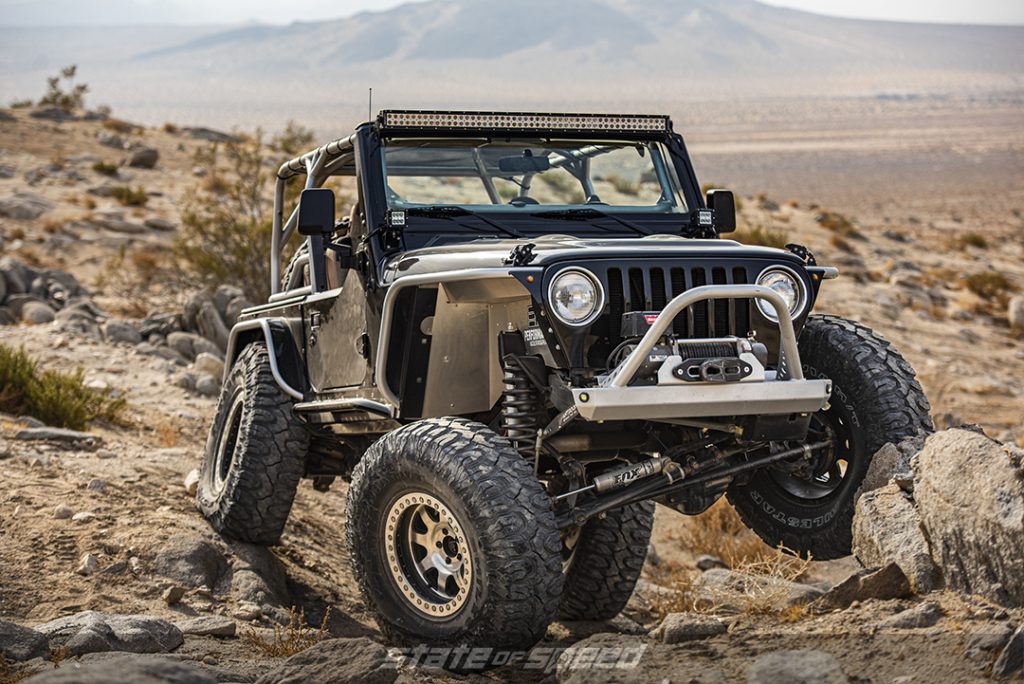
Tires: Milestar Patagonia M/T 37X12.50R17LT
For most the first step is to replace the factory ring and pinion (gear set) with one that provides a lower drive ratio. How low of a drive ratio you choose to install is determined by how you intend to use your 4wd. At minimum you want to install a gear set that lowers your gearing enough to match the final drive ratio your vehicle came equipped with from the factory. Matching the factory final drive ratio will return the performance lost by installing larger tires, yet in most cases it isn’t enough to noticeably improve the vehicles off-road capability. To do that we need to increase the torque being delivered to the tires as well as increase (lower) the vehicles crawl ratio. The simplest way to do that is to install an even lower ratio gear set. How low of a gear ratio you choose can often be limited to the type and model axles your vehicle is equipped with, but for most applications gears in the 4.56:1 or 4.88:1 (higher the number the lower the gear ratio) are the most common for vehicles with tires up to 37” diameter.
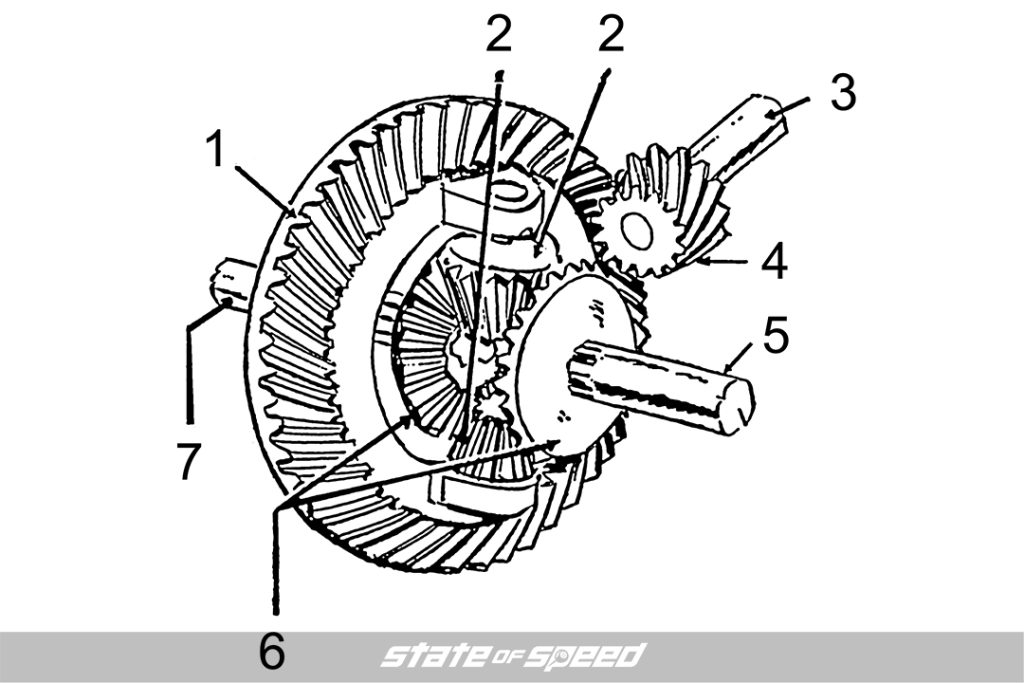
…additional tire size and weight create more stress on the suspension and drive axles...
…additional tire size and weight create more stress on the suspension and drive axles...
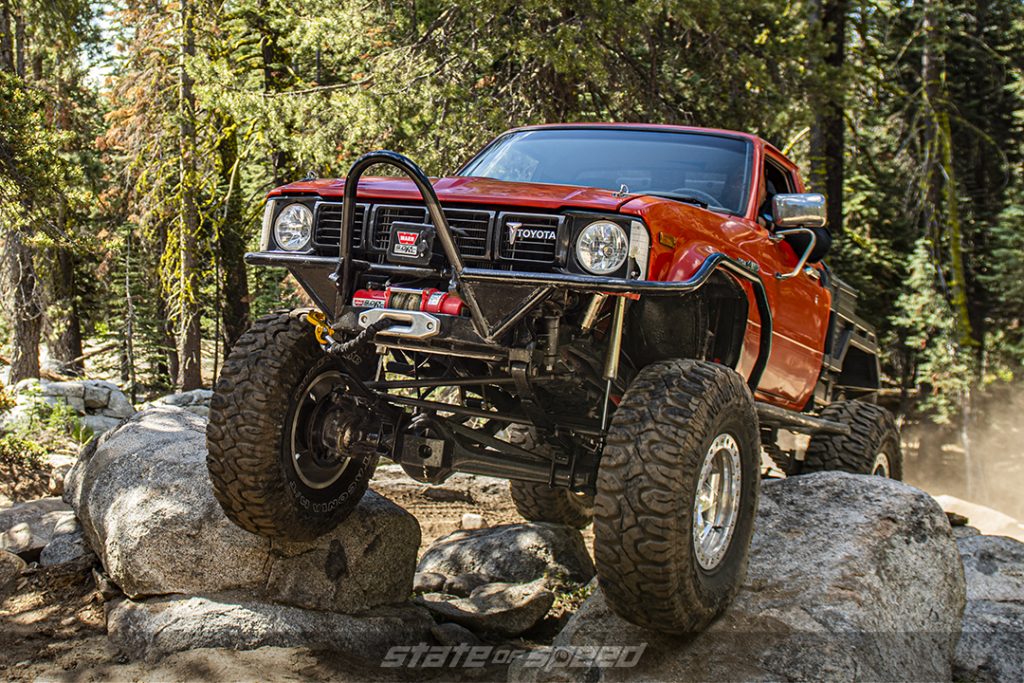
Tires: Milestar Patagonia M/T 37×12.50R17 LT
Before you spend your money on replacing the axle gears, there is another upgrade to take into consideration that can be installed at the same time as your new axle gears. With few exceptions, the drive axles in your 4wd vehicle are equipped with an open differential. The differential is a component that consists of a carrier housing, that is driven by the ring gear, containing a set of gears known as spider gears which in turn drive the axle shafts. When traveling in a straight line the tires are turning at the same speed and equal power is transferred to both drive axles. However, when you turn, the outside tire has to travel a further distance than the inside. To accomplish this the spider gears inside the carrier, allow the outside tire to turn faster than the inside tire. While this design is great for most driving situations, it doesn’t lend itself to low traction situations because it allows the power to be transferred to the tire with the least amount of resistance. To increase a vehicle’s off-road prowess, replacing the factory differential with a mechanical traction control device, more commonly known as a locker can be extremely beneficial.
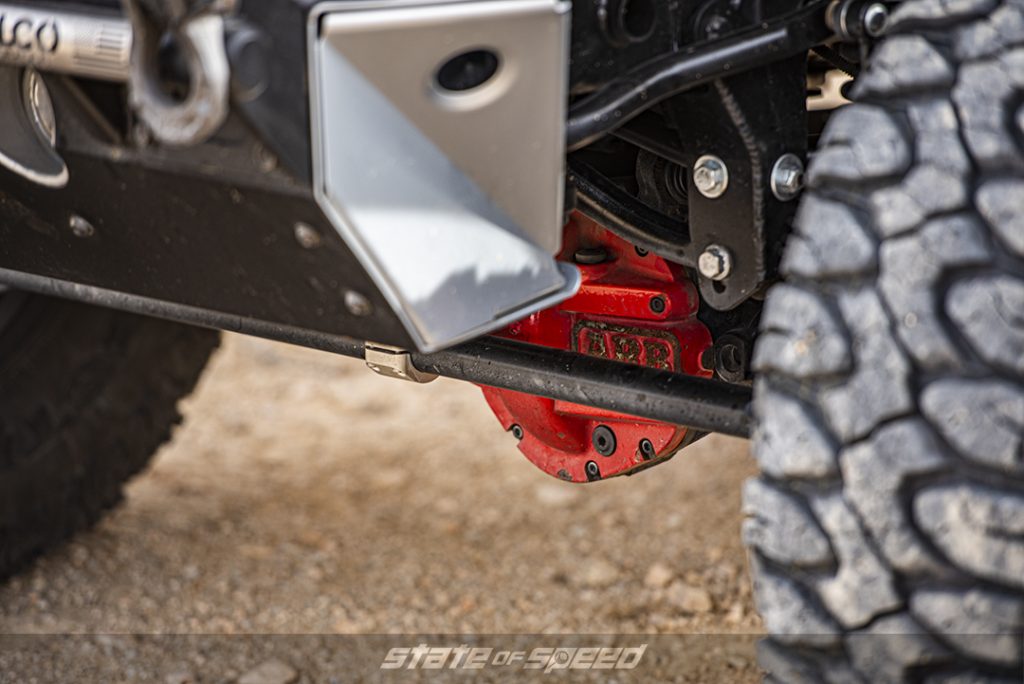
Tires: Milestar Patagonia M/T 38×13.50R17 LT
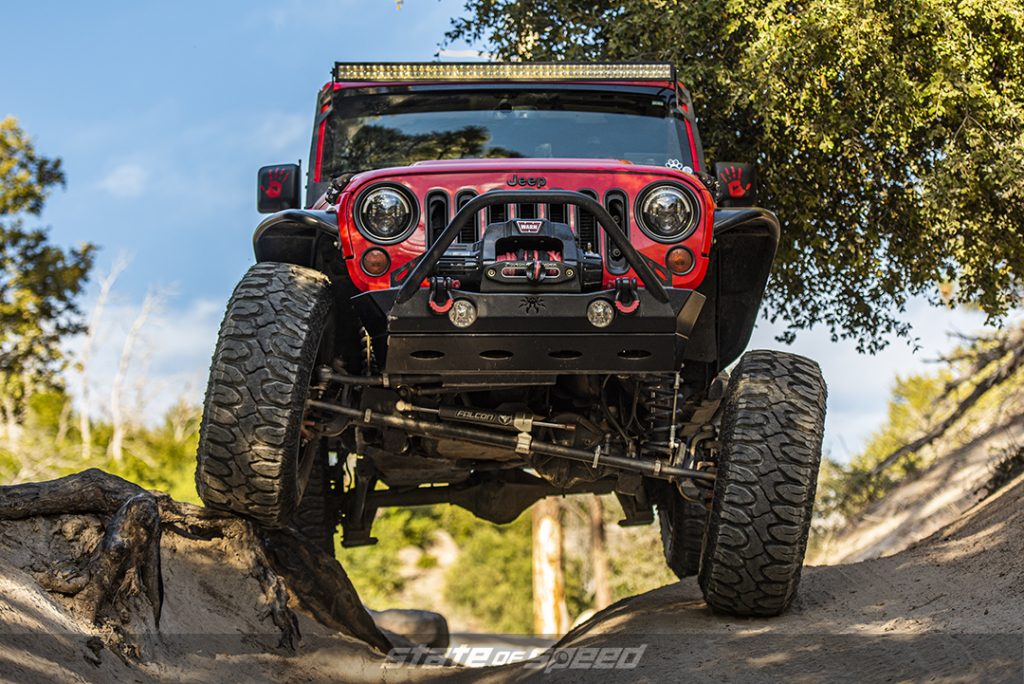
Tires: Milestar Patagonia M/T 37X12.50R17LT
There are multiple options to choose from when it comes to lockers. The cheapest and most basic is the drop in or “lunch box” locker. The lunch box locker simply replaces the factory spider gears with specially machined interlocking components that engage (lock) when power is applied and disengage (unlock) when coasting. The design allows equal torque to be applied to the axles anytime the vehicle is under power. They are however only as strong as the factory cast iron carrier and are known to create erratic handling characteristics on pavement. Due to these characteristics, most people choose to only run them in the front axle which is typically disengaged when driving on the pavement. The next level up is the full case mechanical locker. More commonly referred to as the Detroit locker. These lockers replace the factory carrier and spider gears with a complete unit made from much stronger materials. The overall design functions similar to a lunch box locker and can lead to handling issues if used on the street. Most people choose to limit the installation of Detroit’s to vehicles that see very little road use. The most expensive option is the selectable locker. Available in electric, air, or cable actuation, selectable lockers give the owner the best of both on and off-road traction and handling. Similar to a Detroit, a selectable locker completely replaces the factory carrier. Once installed, they operate very similar to a factory open differential until the owner “engages” the locker. Once engaged, a geared collar slides into place and locks the differential creating equal traction to both wheels. Once the added traction is no longer needed, the driver can simply turn off or disengage the locker. Selectable lockers are most often installed in the rear, and are actually becoming more and more common as factory installed options on many current 4wd vehicles, but they work equally as well in the front axle.
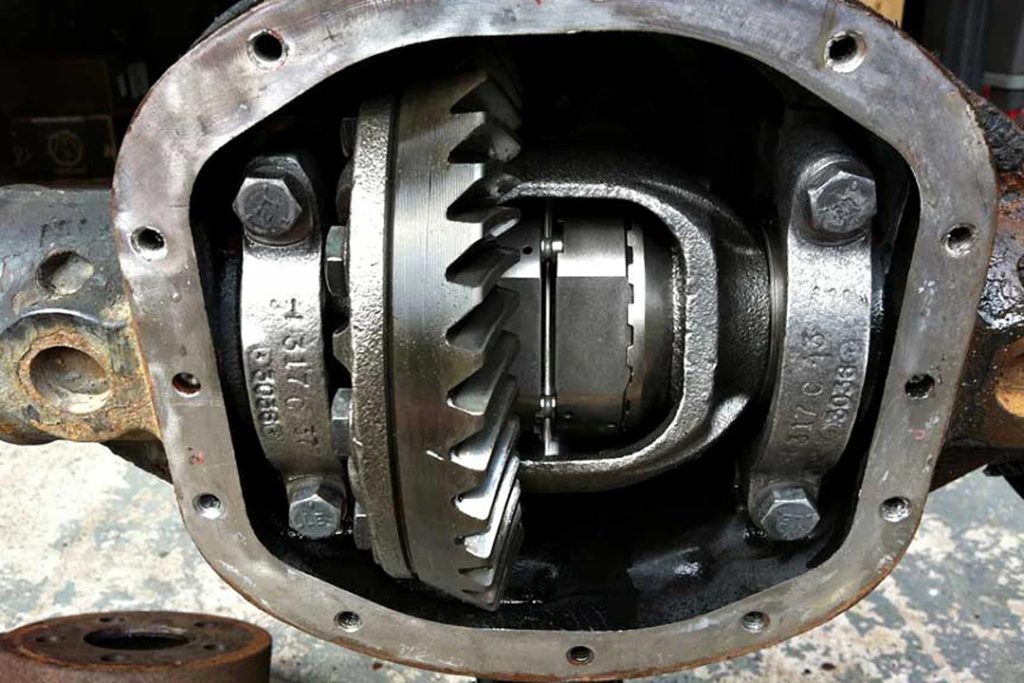
Photo Credit: offroadextreme.com
…Like with most things, the minute you decide to modify something you instantly create a snowball effect where one thing leads to another...
…Like with most things, the minute you decide to modify something you instantly create a snowball effect where one thing leads to another...

Photo Credit: ARB 4×4 Accessories
One of the final things to consider is the drive axles themselves. The factory shafts can typically take a considerable amount of stress, but now that you have increased the leverage necessary to turn a larger diameter tire, compounded the torque applied with lower gears and ensured the power is being transferred to equally despite the load, the axle shafts easily become the next weak link. To overcome this, the aftermarket has created upgraded (stronger) replacement alloy axle shafts. Available in heat treated 4340 chrome molly or 300M materials along with various options of upgraded universal or constant velocity joints, installing aftermarket axle shafts is something that should seriously be considered any time you start upgrading your axles.
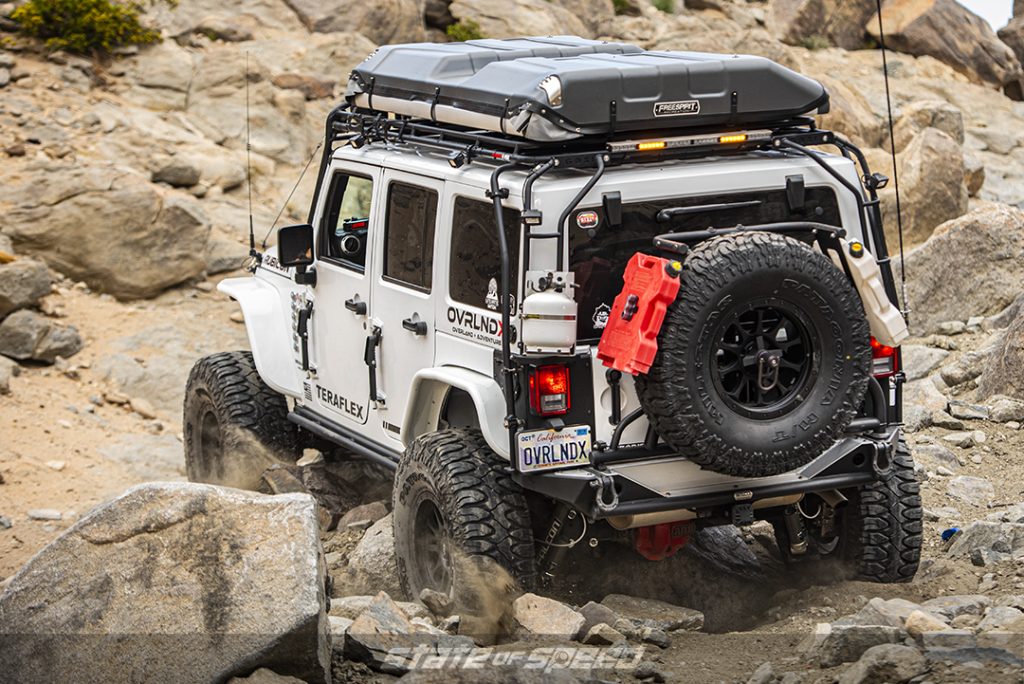
Tires: Milestar Patagonia M/T 38×13.50R17 LT
Like with most things, the minute you decide to modify something you instantly create a snowball effect where one thing leads to another. When it comes to 4wd vehicles, bigger tires and the desire to explore the road less traveled often leads to the need to upgrading the axles. If you are planning to upgrade your 4wd, you may soon find yourself in the same situation. When the time comes, we highly recommend talking to your local off-road shop or one of the businesses that specialize in the particular make and model of your vehicle. They can help you plan ahead and know exactly what and when you need to upgrade.